The project was carried out for one of the largest bulb and lamp manufacturers in Poland. The task of the system is to control the correctness of the product and the correctness of the printing on the bulb element.
The system consists of a single station equipped with four cameras and eight illuminators. Each camera is responsible for inspecting one of the four sides of the workpiece on the conveyor.
After the inspection, the cameras report the detected defects to the PLC (a total of 15 OK/NOK results).
The scope of control:
– X angle of the electrode
– Electrode milling
– Presence of pinch
– Y angle of the electrode
– Presence of front printing
– Presence of shell clips
– Presence of domino marking
– Presence of rear printing
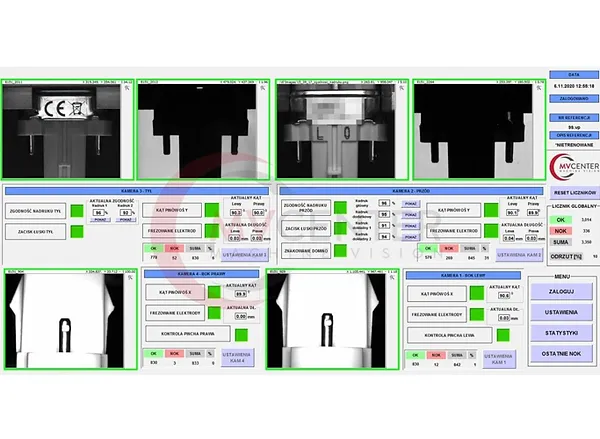