What is the TPV company?
TPV Displays Poland is a manufacturer of LCD and OLED TVs and SSBs. It specializes in manufacturing activities in the form of ODM and OEM, and develops its own brands. It has ten assembly lines for televisions and three lines producing printed circuit boards.
The Gorzow factory is a leader in the production of LCD and OLED monitors in Europe, and thanks to cooperation with the Philips corporation, also in the design and assembly of these devices.
TPV Display Poland’s problem
A major problem for TPV Display Poland is the inadequate connection of cables to motherboards, power supplies and panels. This can cause problems in the operation of our manufactured equipment.
In addition, it happens that the quality control department also fails to notice such errors as the absence of some mounting screws or the routing of cables in mounting hole locations.
A costly process of disassembling receivers is required if a defect is detected on one piece from a production batch, and inspecting the entire batch if an error is detected in just one product.
A human working 8 hours cannot control the correctness of assembly with the same repeatability as a machine. The company wants to immunize itself against imperfections in the work of the crew. It does not intend to lay off employees, but it must ensure the quality of products delivered to the market.
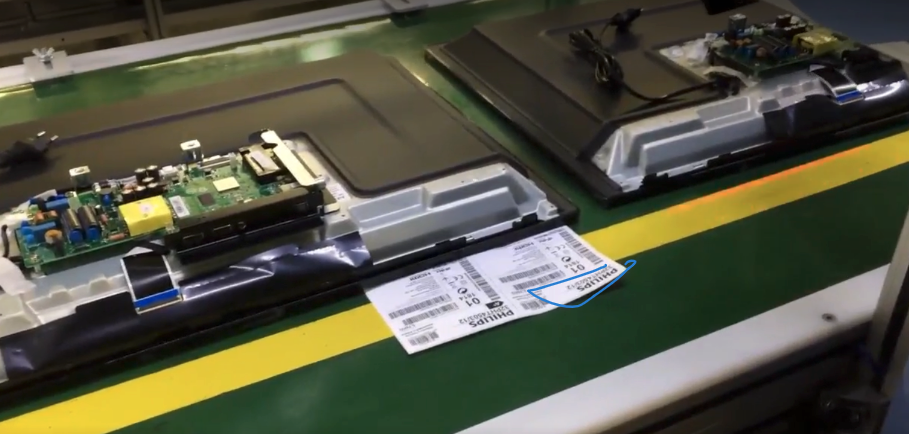
How did we solve the Partner’s problem?
Since no two deployments and production lines are the same, we started our work as usual by building from a pilot station, which we wanted to prove ROI with first.
Wanting to relieve employees of manual quality control and at the same time increase the efficiency of this process with the help of machine vision, we were already building, developing and optimizing a dedicated system in 2016. It has grown from a single station to a solution that is being systematically introduced into all 9 production lines. Thus automating video inspection among all the TVs produced at the plant.
The use of the solution also allows the station to adapt smoothly to changing types of receivers (e.g., different barcode locations and different sizes, thickness of passing TVs).
The software supporting the solution also allows the definition of a virtually unlimited number of controlled elements and their combinations. The solution is 100% editable and flexible even without knowledge of a programming language!
Examples of items verified by the system:
- presence of mounting screws
- correct position of cable mounting tapes
- checking free areas and VESA pins (no cables near them)
- connector fastening
- LVDS tape fastener
- the correctness of the wiring
The software allows you to define your own control schemes, change speed settings and adapt to different types of assembly lines. The system also stores an archive of images from each completed inspection (with no limit on the size of the history), allowing us to verify backwards any batch number with the accuracy of a single screw.
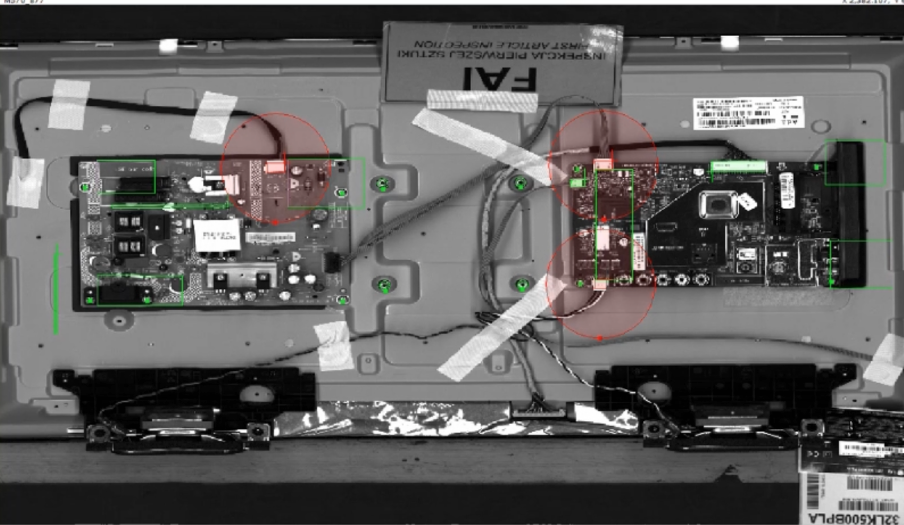
Results of the project
✅ | Ability to redirect quality control employees to more difficult activities |
✅ | 150% faster quality control and production improvement |
✅ | Approximately £20k per month saved on defective products – ROI paid back 100% |
✅ | Implementation successfully completed on 9 lines in Gorzow |
✅ | Adaptability of the solution to changes in the production process |
Customer Quote
“We invested in equipment from MV-Center – we built it with a company from KRAKOW, MV-center provided the vision systems – these systems allow us to be immune to the imperfections of the employees’ work.”
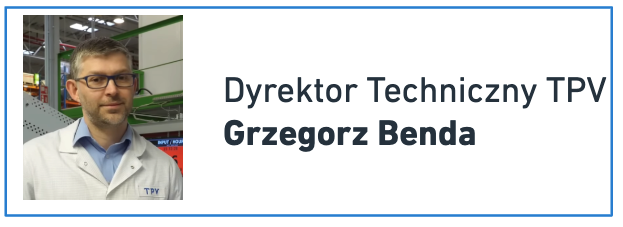
Summary
The entire project included the delivery of 9 complete stations for vision inspection of TV components. After ordering the first pilot station in 2016, testing it and optimizing it, the customer decided to order 8 more stations.
An honorable mention for us was given by the Technical Director of the TPV factory himself, Mr. Grzegorz Benda, who, in the pages of the hdtvpolska portal, spoke of us as the team from Krakow that helped them implement the system.
The material is available below:
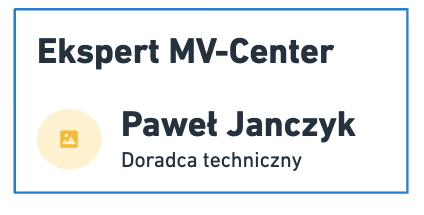