MV Center Vision Systems engineers have developed a semi-automatic EGR pipe geometry measurement station. The workstation was equipped with a rotary table including a mounting socket and a cage for a precision (+/- 0.02 mm positioning accuracy) MITSUBISHI RV-7FLM robot.
An execution unit for the measurement – a GOCATOR 2340 3D scanner – was installed on the robot’s effector. The task of the layout was:
- Quality control of the input and output flanges of the cable (flatness inspection),
- The position of the embossments on the pipe with respect to the measuring base (input flange),
- Control of the position of mounting elements (hooks, handles, pressure probe) in 3D space with respect to the same base,
- Control of the position of the input flange surface to the output flange;
The cycle time of the position is approx. 60 seconds during which measurements are taken at more than 20 reference points and 3 surfaces (flanges + handle) are scanned. The stand supports 3 references, each detail is marked with an individual QR code and the measurement report is generated in PDF format. NOK details are blocked in the superordinate system and must be deposited by the operator in a special shortage zone.
EGR pipe inspection report.
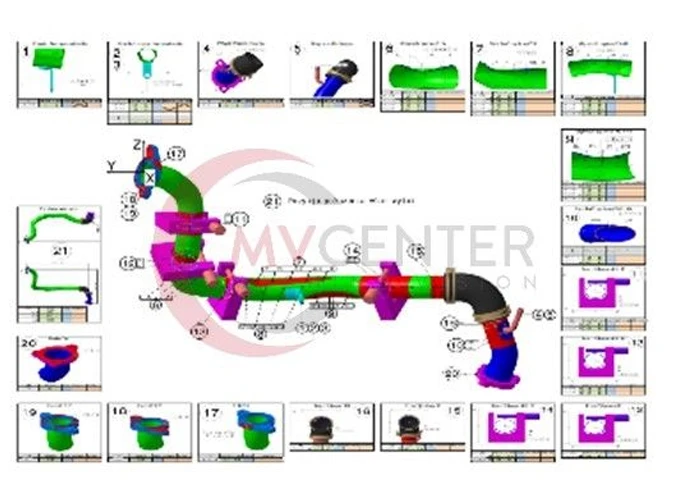
Checking the geometry of the EGR pipe
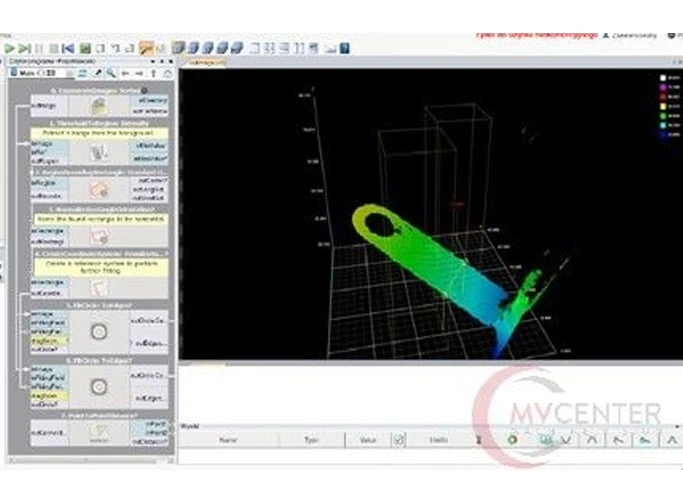
Checking the geometry of the EGR pipe
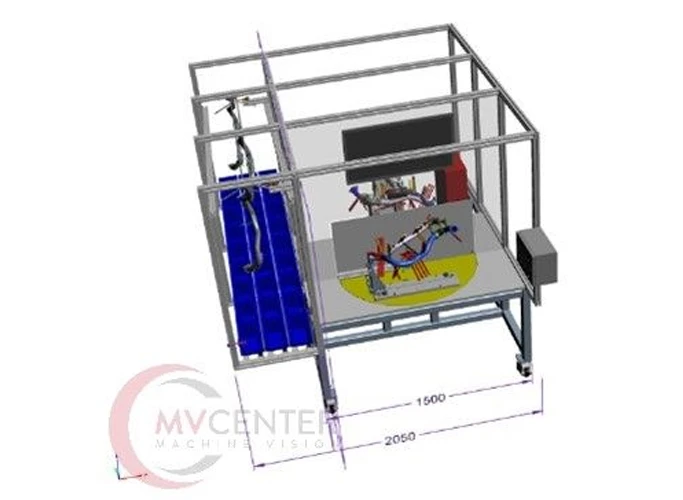